A cerâmica de nitreto de alumínio é um importante material de substrato para dissipação de calor, mas o substrato cerâmico de nitreto de alumínio em si não possui condutividade elétrica, portanto a superfície deve ser metalizada antes de ser usada como substrato de dissipação de calor de alta potência.
A capacidade de umedecimento do metal na superfície cerâmica em alta temperatura determina a força de ligação entre o metal e a cerâmica, e uma boa força de ligação é uma garantia importante para a estabilidade do desempenho da embalagem. Portanto, a realização da metalização do substrato cerâmico é uma parte importante da aplicação prática da cerâmica de nitreto de alumínio.
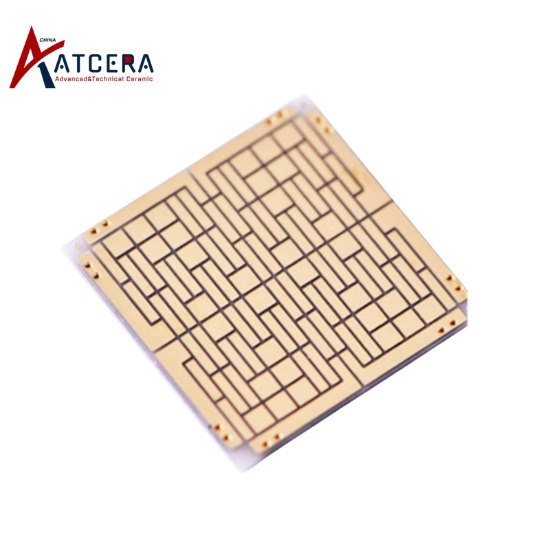
Conexão Mecânica e Colagem
O método de conexão mecânica é caracterizado pela adoção de um projeto estrutural razoável e pelo uso de tensão mecânica para realizar a conexão entre o substrato de nitreto de alumínio e o metal, como conexão de luva quente e conexão de parafuso. O método de conexão mecânica possui características de processo simples e boa viabilidade, mas a tensão na conexão é grande, não é adequado para ambientes de alta temperatura e a faixa de aplicação é limitada.
A ligação refere-se ao aglutinante orgânico como meio de conexão, através do processo de ligação apropriado, a natureza do substrato de nitreto de alumínio e materiais metálicos combinados em um método de conexão mecânica completa. No entanto, o método de ligação também não é adequado para ambientes de alta temperatura e alta resistência, e a faixa de uso é pequena.
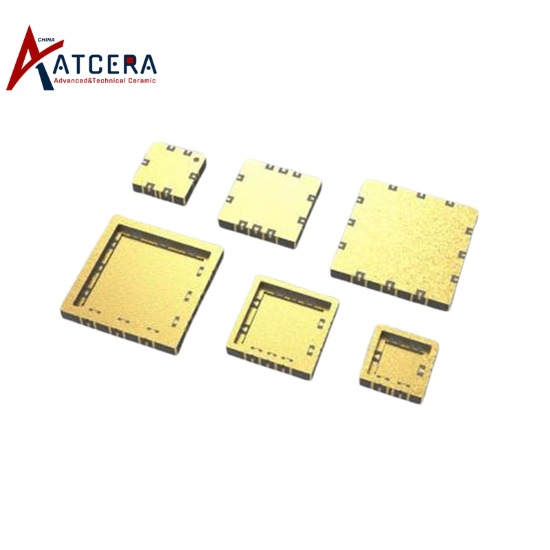
Método de Filme Espesso (TPC)
O método de filme espesso refere-se ao processo de revestimento direto de uma pasta condutora na superfície do substrato cerâmico de nitreto de alumínio por meio de serigrafia e, em seguida, secagem e sinterização em alta temperatura para fazer o revestimento metálico aderir à superfície do substrato cerâmico.
A pasta condutora é geralmente composta de pó metálico condutor, aglutinante de vidro e transportador orgânico. O pó metálico condutor determina as propriedades elétricas e mecânicas da pasta após a formação do filme, e os pós metálicos comumente usados são prata, cobre, níquel e alumínio, etc., dos quais prata e cobre têm baixa resistência e baixo custo, e são mais adequado para produção industrial.
Portanto, o processo é confiável, tem as vantagens de alta eficiência de produção, baixo custo e design flexível. Sua desvantagem é que é limitado pela precisão do processo de serigrafia, a adesão não é fácil de controlar e o substrato sinterizado não consegue obter linhas de alta precisão, portanto só pode ser aplicado em materiais de embalagem de dispositivos eletrônicos com baixa linha requisitos de precisão.
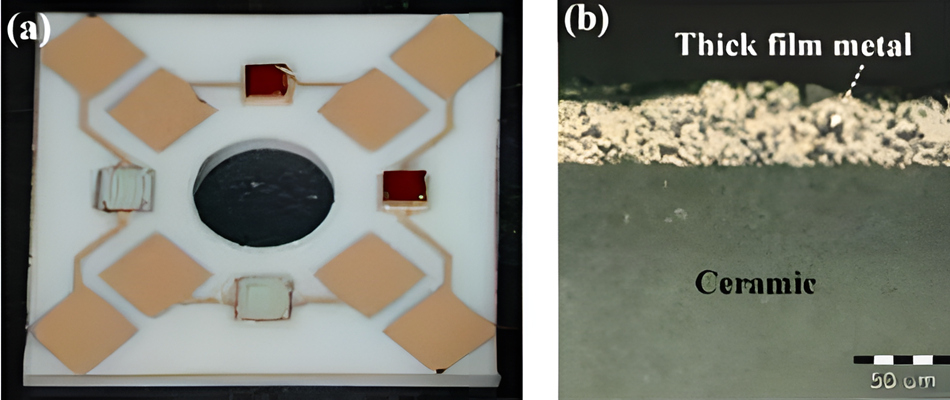
Brasagem de Metal Ativo (AMB)
O método de brasagem de metal ativo consiste em adicionar diretamente Ti, Zr, Al, Nb, V e outros elementos de transição com propriedades químicas relativamente ativas ao metal de brasagem comum. Esses elementos ativos reagem quimicamente diretamente com a superfície da cerâmica de nitreto de alumínio para formar uma camada de transição, o principal produto da camada de transição são alguns compostos de ligação metálica e tem a mesma estrutura do metal, para que possa ser umedecido pela carga derretida metal para formar uma junta metalúrgica.
O substrato cerâmico de nitreto de alumínio é um importante dispositivo de dissipação de calor, frequentemente usado em altas temperaturas, portanto, são necessárias mais juntas de alta temperatura. O metal de brasagem ativo de alta temperatura composto principalmente de CuTi e NiTi pode ser usado na faixa de 1200 ~ 1800 ℃. O metal de brasagem de sistema ternário ou sistema multicomponente representado por metal de brasagem à base de Au, base de Co e base de PD é o metal de brasagem ativo de alta temperatura mais comumente usado. O ponto de fusão do Au, Co e Pd é 1064°C, 1492°C e 1554°C respectivamente, o que desempenha um papel no aumento do ponto de fusão no metal de brasagem.
Como os elementos ativos do metal de brasagem são quimicamente ativos, para evitar reações químicas com o oxigênio em altas temperaturas, a brasagem ativa deve ser realizada sob a proteção de um ambiente severo de vácuo ou de uma atmosfera inerte, e o custo técnico é alto , e não é adequado para aplicações em grande escala.
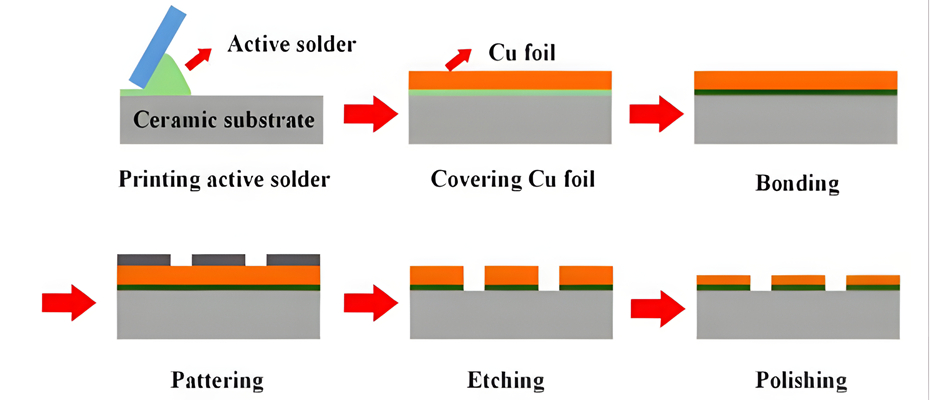