No campo dos materiais de alta tecnologia, a cerâmica de nitreto de alumínio (AlN), com sua excelente condutividade térmica, excelentes propriedades de isolamento elétrico e excelente resistência mecânica, tornou-se o material central em campos-chave como embalagens eletrônicas, eletrônica de potência e equipamentos de comunicação por microondas. . No entanto, a preparação do substrato de nitreto de alumínio é um processo complexo, no qual o processo de sinterização e a seleção dos aditivos de sinterização têm efeitos importantes nas propriedades do produto final. Neste artigo, a partir do processo de preparação do substrato cerâmico aln, a seleção dos aditivos de sinterização e sua influência no desempenho do substrato serão discutidas em detalhes e, combinadas com pesquisas de fronteira, como melhorar o desempenho abrangente do substrato de nitreto de alumínio otimizando os aditivos de sinterização e o processo de sinterização serão analisados.
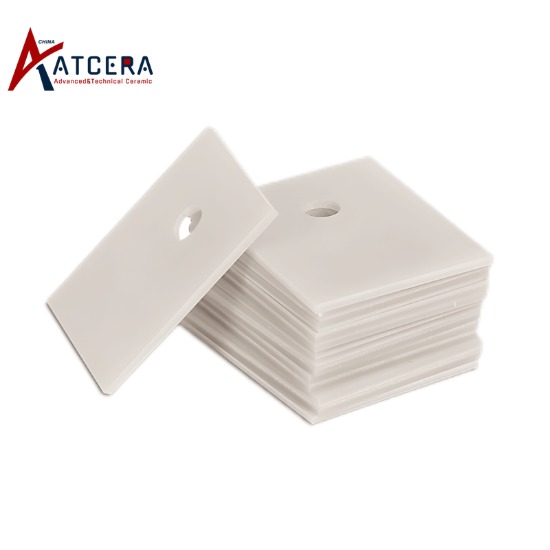
Tecnologia de preparação de substrato de nitreto de alumínio
A preparação do substrato de nitreto de alumínio inclui principalmente a preparação da matéria-prima, mistura, moldagem, sinterização e outras etapas importantes.
1. Preparação de matéria-prima
A preparação da matéria-prima é a primeira etapa na preparação do substrato cerâmico de nitreto de alumínio, que inclui principalmente a seleção e proporção de pó de nitreto de alumínio, pó de alumina e aditivos. Como material principal, o pó de nitreto de alumínio deve ter características de alta pureza, tamanho de partícula pequeno, grande área de superfície específica, baixo teor de carbono e baixo teor de oxigênio. O pó de alumina é geralmente usado como parte do auxiliar de sinterização para formar um óxido composto de baixo ponto de fusão durante o processo de sinterização para promover a densificação da cerâmica de nitreto de alumínio. Os aditivos são usados para regular as propriedades de moldagem, propriedades de sinterização e propriedades mecânicas do material.
2. Misture e forme
No processo de mistura, é necessário misturar pó de nitreto de alumínio, pó de alumina e aditivos de acordo com uma determinada proporção para garantir a uniformidade e estabilidade da moldagem subsequente. A mistura pode ser feita pelo método seco ou úmido. A moldagem geralmente é feita por prensagem, moldagem por injeção ou moldagem sob pressão, etc., as matérias-primas misturadas são transformadas em tarugos com um determinado formato e tamanho.
3. Sinterização
A sinterização é o último processo e a etapa mais crítica na preparação do substrato cerâmico de nitreto de alumínio. Sob condições de alta temperatura, as partículas do tarugo são combinadas por sinterização para formar um substrato cerâmico denso. No processo de sinterização, a temperatura, a atmosfera e o tempo precisam ser controlados para garantir a qualidade de formação e o desempenho do substrato cerâmico. Os processos de sinterização comumente usados incluem sinterização por prensagem a quente, sinterização sem prensagem, sinterização por microondas, sinterização por plasma de descarga e sinterização autopropagada.
A seleção de aditivos de sinterização e sua influência nas propriedades do substrato
Os aditivos de sinterização desempenham um papel importante na preparação de substratos cerâmicos de nitreto de alumínio. Eles reagem com a composição de alumina na superfície da partícula de nitreto de alumínio para formar um óxido compósito com baixo ponto de fusão, resultando em uma fase líquida no corpo sinterizado. Essas fases líquidas circundam as partículas de nitreto de alumínio, e o rearranjo das partículas e a descarga interna dos poros ocorrem sob a ação da força capilar e, finalmente, a sinterização compacta da cerâmica de nitreto de alumínio é realizada.
1. Aditivos de sinterização comumente usados
Os auxiliares de sinterização comumente usados para substratos cerâmicos de nitreto de alumínio incluem CaO, Li2O, B2O3, Y2O3, CaF2, CaC2 e CeO2. Esses materiais desempenham um papel duplo no processo de sinterização: primeiro, combinam-se com o óxido de alumínio na superfície das partículas de nitreto de alumínio para formar aluminato líquido, acelerando a transferência de massa e promovendo a sinterização; Em segundo lugar, eles podem reagir com o oxigênio para reduzir o teor de oxigênio da rede e aumentar a condutividade térmica da cerâmica de nitreto de alumínio.
2. Princípio de seleção de aditivos de sinterização
Ao selecionar aditivos de sinterização, é necessário considerar sua influência nas propriedades do substrato cerâmico de nitreto de alumínio. Por um lado, os aditivos de sinterização devem promover a densificação da cerâmica de nitreto de alumínio, melhorar a condutividade térmica e a resistência mecânica; Por outro lado, os aditivos de sinterização devem evitar a introdução de impurezas excessivas, de modo a não afetar as propriedades de isolamento elétrico e a estabilidade química da cerâmica de nitreto de alumínio. Portanto, ao selecionar aditivos de sinterização, são necessários muitos experimentos e otimizações para determinar a melhor fórmula de aditivos de sinterização.
3. Influência dos aditivos de sinterização no desempenho do substrato
A seleção e o conteúdo dos aditivos de sinterização têm influência significativa no desempenho do substrato cerâmico de nitreto de alumínio. Por exemplo, Y2O3, como um dos aditivos de sinterização comumente usados, pode melhorar significativamente a condutividade térmica e a resistência à flexão da cerâmica de nitreto de alumínio quando o conteúdo é moderado. Porém, quando o teor de Y2O3 é muito alto, a fase Y-Al-O será formada, resultando em uma diminuição significativa na condutividade térmica. Portanto, ao preparar substrato cerâmico de nitreto de alumínio, é necessário controlar com precisão o teor de aditivos de sinterização para obter o melhor desempenho.
Melhor desempenho do substrato AlN
Para atender aos altos requisitos de desempenho de substratos cerâmicos de nitreto de alumínio em diferentes campos de aplicação, os pesquisadores estão constantemente explorando novos aditivos de sinterização, otimizando processos de sinterização e desenvolvendo novas tecnologias de preparação.
1. Desenvolvimento de novos aditivos de sinterização
A fim de melhorar ainda mais o desempenho dos substratos cerâmicos de nitreto de alumínio, os pesquisadores estão desenvolvendo ativamente novos aditivos de sinterização. Por exemplo, ao introduzir elementos de terras raras ou elementos de metais de transição, a estrutura reticular da cerâmica de nitreto de alumínio pode ser otimizada para melhorar a condutividade térmica e as propriedades mecânicas. Além disso, uma variedade de propriedades pode ser alcançada através do uso de aditivos de sinterização composta.
2. Otimização do processo de sinterização
A otimização do processo de sinterização é a chave para melhorar o desempenho do substrato cerâmico de nitreto de alumínio. Ao ajustar a temperatura de sinterização, o tempo de retenção e a atmosfera, a microestrutura da cerâmica de nitreto de alumínio pode ser controlada com precisão. Por exemplo, métodos de sinterização rápida, como sinterização por microondas ou sinterização por plasma de descarga, podem reduzir significativamente o tempo de sinterização e melhorar a eficiência da produção. Ao mesmo tempo, a microestrutura e as propriedades da cerâmica de nitreto de Al podem ser ainda mais otimizadas controlando com precisão o teor de oxigênio e o gradiente de temperatura na atmosfera de sinterização.
3. Inovação da tecnologia de preparação
Com o desenvolvimento contínuo da tecnologia de preparação, os pesquisadores estão constantemente explorando novos métodos de preparação para melhorar o desempenho dos substratos cerâmicos de nitreto de alumínio. Por exemplo, a preparação precisa do substrato cerâmico de nitreto de alumínio pode ser alcançada usando tecnologias de moldagem avançadas, como moldagem por fundição e moldagem por injeção. Além disso, o desempenho de soldagem, a estabilidade e a resistência à corrosão do substrato cerâmico de nitreto de alumínio podem ser melhorados ainda mais por revestimento de cobre sem eletrólito, encapsulamento de substrato cerâmico e outros processos de pós-tratamento.
Conclusão
Em resumo, a preparação do substrato cerâmico de nitreto de alumínio e a seleção dos aditivos de sinterização têm efeitos importantes nas suas propriedades. As propriedades abrangentes do substrato cerâmico de nitreto de alumínio podem ser significativamente melhoradas otimizando a fórmula auxiliar de sinterização, melhorando o processo de sinterização e desenvolvendo novas tecnologias de preparação. No futuro, com o desenvolvimento contínuo da ciência dos materiais e da tecnologia de preparação, o campo de aplicação do substrato cerâmico de nitreto de alumínio será ainda mais expandido, fornecendo forte apoio para o desenvolvimento de embalagens eletrônicas, dispositivos eletrônicos de potência e equipamentos de comunicação por microondas. Ao mesmo tempo, também precisamos prestar muita atenção à tendência de desenvolvimento de novas tecnologias e novos materiais, expandir constantemente o horizonte de pesquisa e promover o progresso contínuo e a inovação da tecnologia de substrato cerâmico de nitreto de alumínio.